What is HBOX™?
The HBOX™ system is an arrangement of tubes and joints, which together form a framework. There are no welds between the connecting pieces in the system, instead the parts are fixed together using the force of friction. Dowel Pins can be used to mechanically lock the system.
HBOX™ units are used to join standard tubes to form the framework of the jig. The framework is set to a loose tolerance facilitating a quick assembly process and the use of standard low cost beams. The final accurate interface between the jig and the component is achieved through adjustable HFLAG™ and HSHIMBOX™ units.
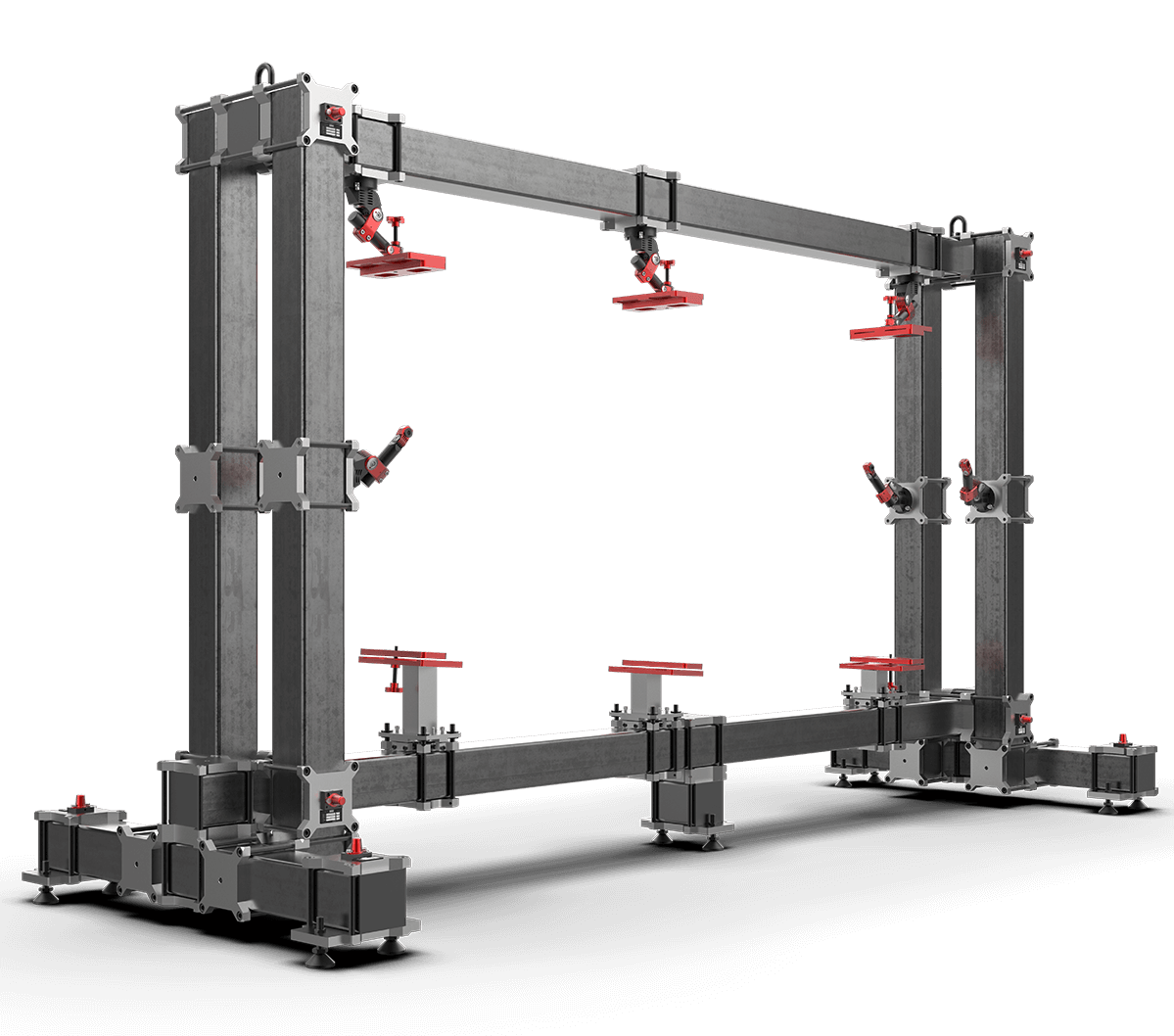
Key Components
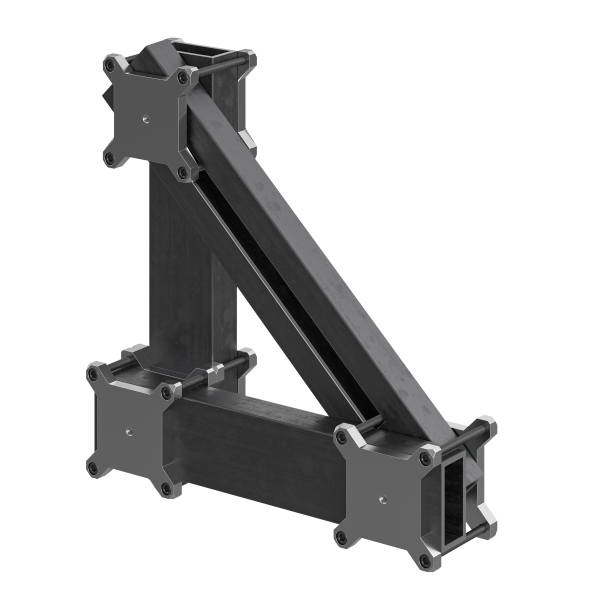
HBOX™
HBOX™ creates a structure fast by utilizing off-the-shelf aluminum, steel, or carbon fiber beams joined with plates and bolts. Bolts are pulled to a high torque to give a rigid friction joint, equal in stiffness to a weld. HBOX™ eliminates welding and stress reliving on jig frames.
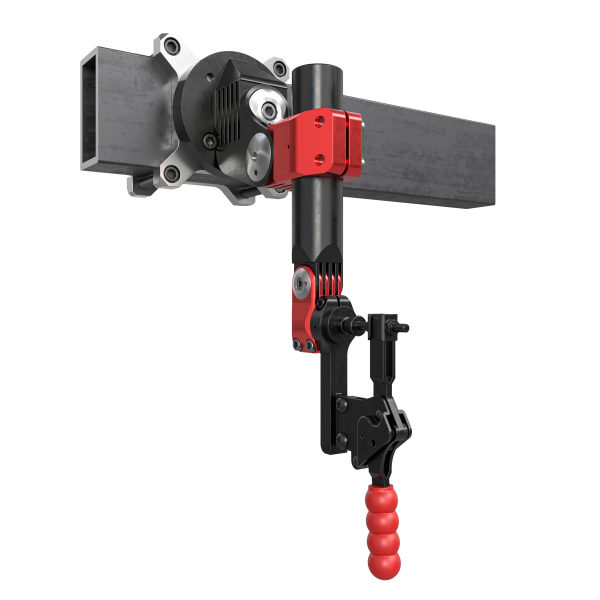
HFLAG™
HFLAG™ is a 6 DOF (degrees of freedom) index that is manually adjusted then locked when the desired location is reached. Standard end-effectors are available for clamps, rest pads, round (4 way), and slotted (2 way) bushings. HFLAG™ eliminates expensive, custom-made risers, locators, shims, etc.
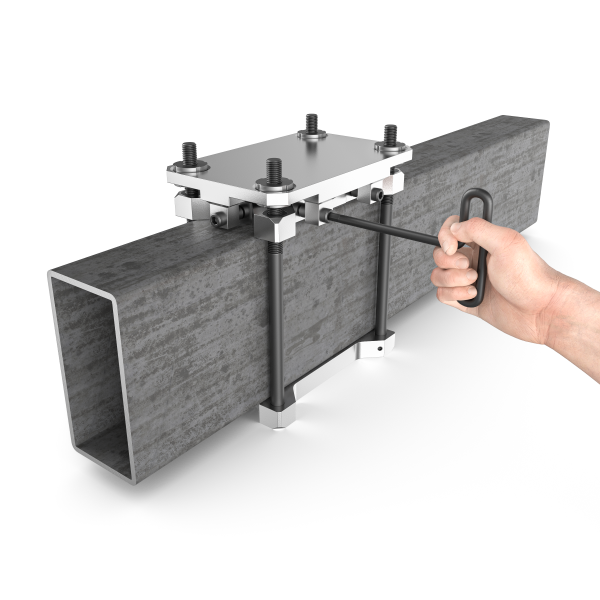
HSHIMBOX™
HSHIMBOX™ technology enables users to integrate drill jigs, header-boards and other high tolerance, fixed tooling into an HBOX™ environment. The top plate of the unit is modified with a mounting pattern for attachment. An operator can set a HSHIMBOX™ into a tight-tolerance position within a few minutes.
Stealth aircraft leverages flexible tooling!
To request the case study about building a cutting-edge stealth aircraft taking advantage of flexible tooling, enter your information below and our team will be in touch with you shortly! Don’t forget to check your spam folder.
"*" indicates required fields
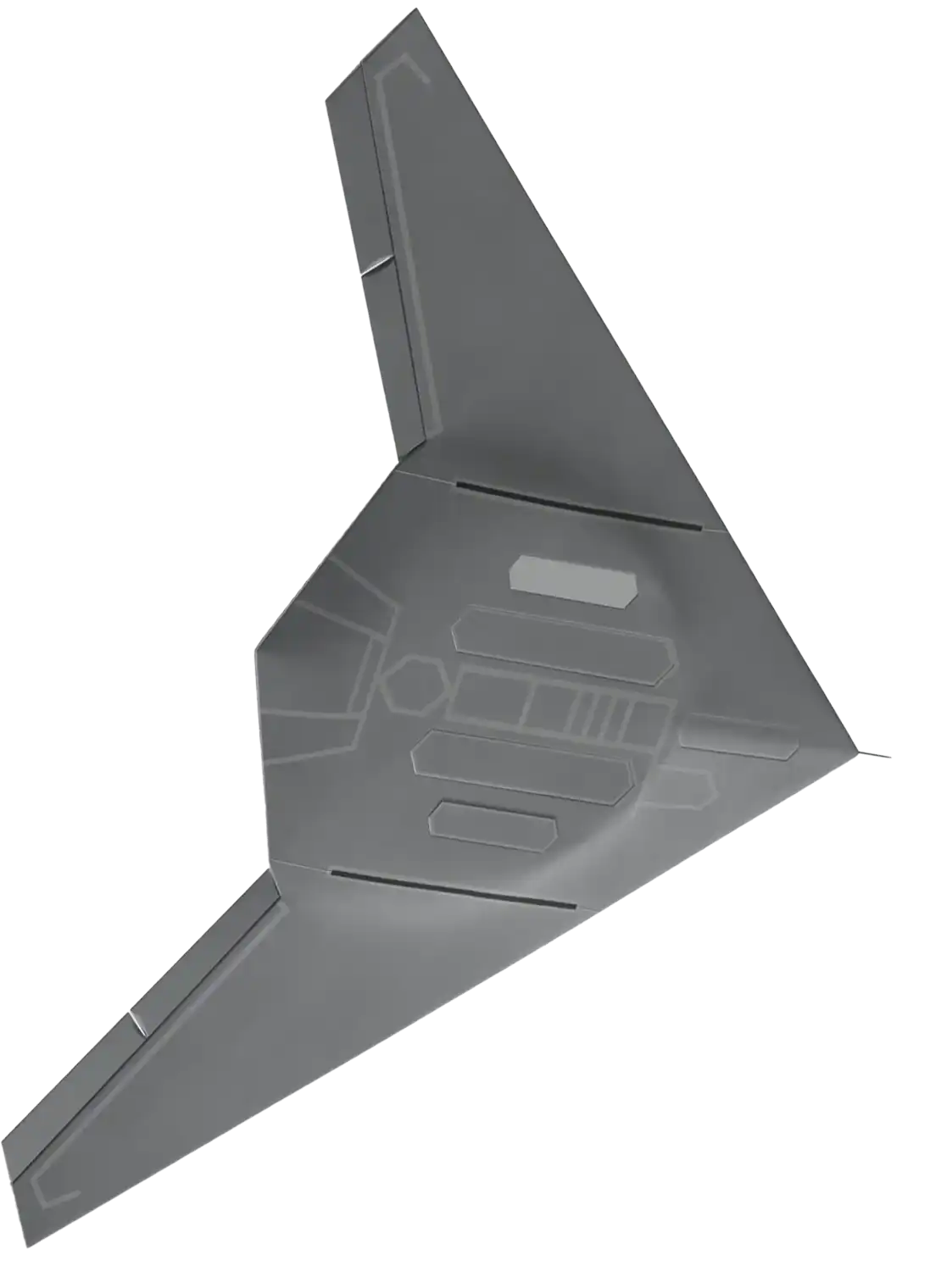
Revolutionizing Manufacturing
Repeatability
Proven in the most demanding production environments in the world.
Material Options
Design to work interchangeably with standard, off-the-shelf tubes in either steel, aluminum, or carbon fiber.
"Lego" Concept
All HBOX™ elements can be reconfigured to absorb design changes or create endless tools. No more tooling boneyards, no more tooling storage costs.
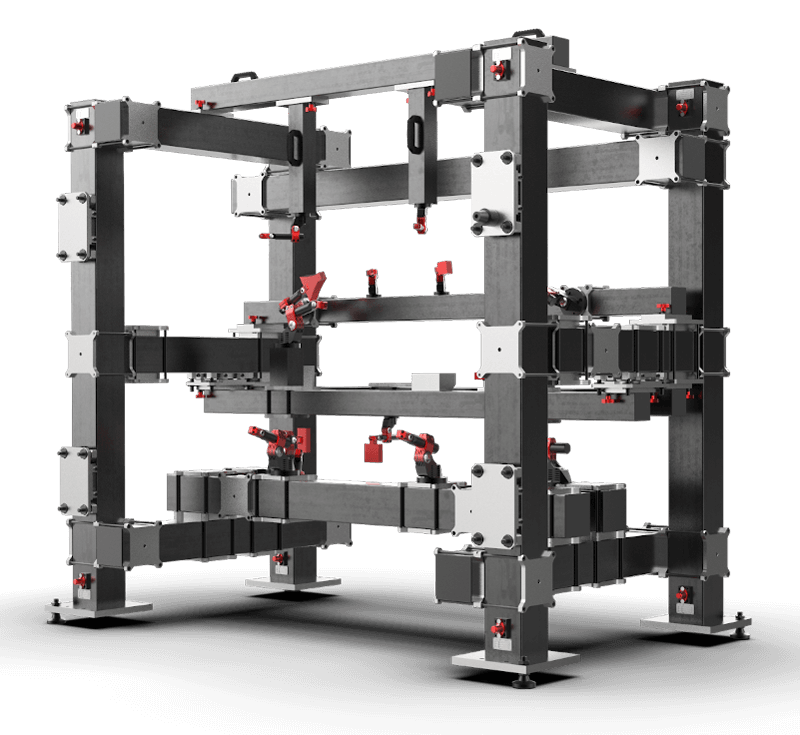
Compatibility
Easily integrate electrical, mechanical, pneumatic systems such as LED lighting, air lines, controls, etc.
Light on your Budget
Faster to design, faster to build, easy to modify, reconfigurable - all translate to costs savings. One third party study proved 80% cost savings when compared to traditional tooling.
Short Lead Times
In stock, easy to assemble and calibrate.
Sweet Spot Analysis
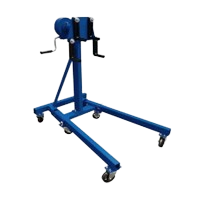
Online Ergo Products
Configurability
–
Cost
Stress Analysis
–
Safety Features
Precision
–
High Production
Lead Time
Quality
Origin
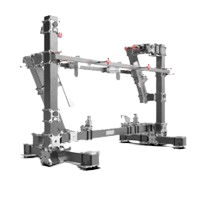
HBOX™ Tooling
Configurability
Cost
Stress Analysis
Safety Features
Precision
High Production
Lead Time
Quality
Origin
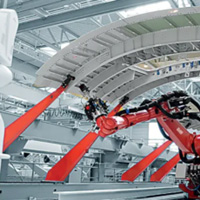
Factory Automation
Configurability
Cost
Stress Analysis
Safety Features
Precision
High Production
Lead Time
Quality
Origin
What Our Customers Say
Approved HBOX™ Integrators
Expert end-to-end support
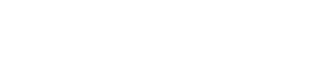
Aciturri Aeronáutica
Headquartered in Michigan, Delivering throughout Europe.
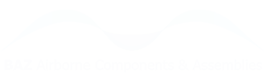
BAZ Aircraft
Headquartered in Israel, Delivering throughout the Middle East.
Want to become an Approved HBOX™ Integrator?
Applications
From the Aerospace to Automotive industries, HBOX™ versatility is limitless. We have worked with hundreds of companies small and large, providing them with customized and engineered tooling solutions for their programs. The modularity of HBOX™ makes it perfect for one-off applications to full assembly lines.
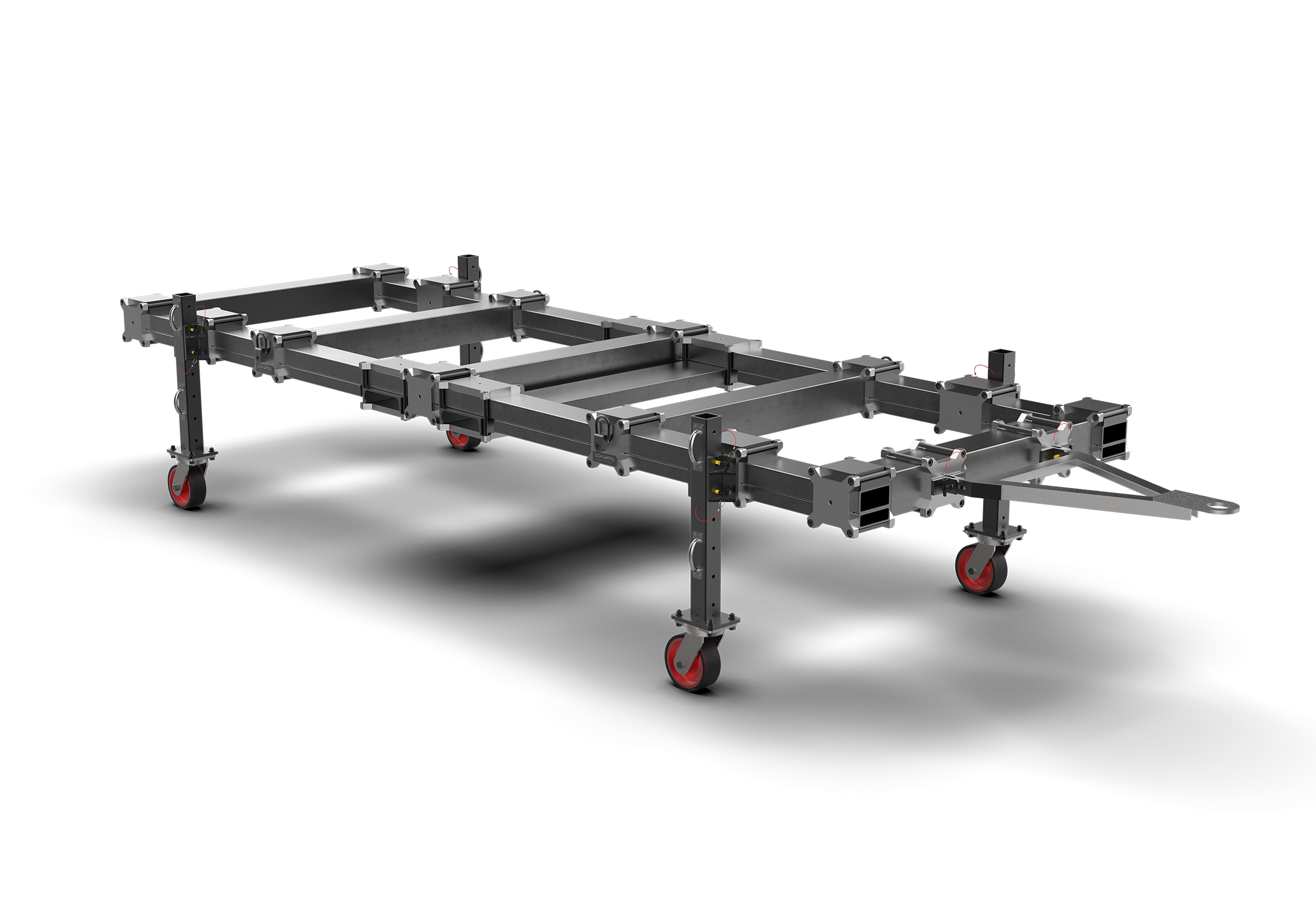
Autoclave Tooling Cart
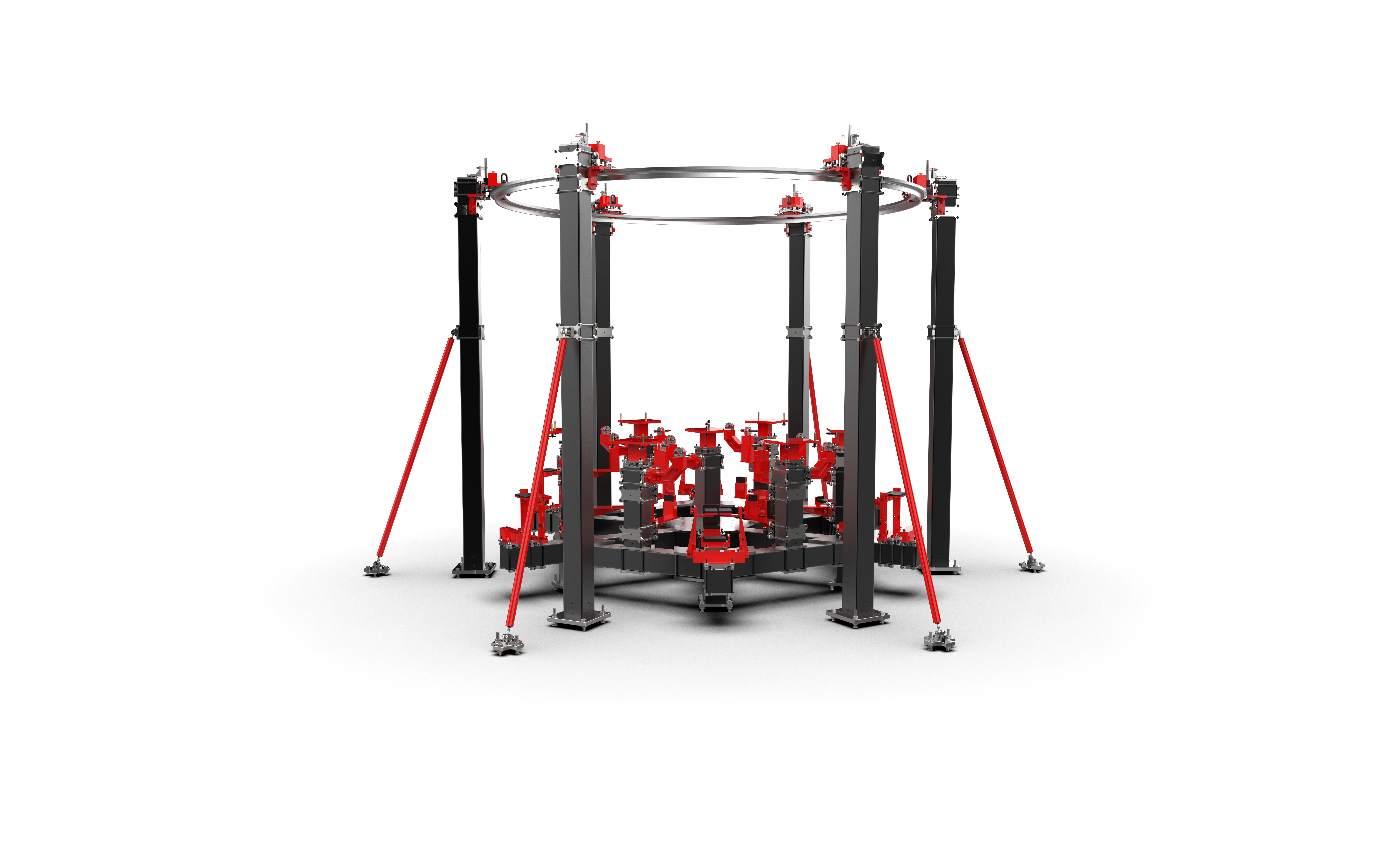
Thrust Structure Assembly Jig
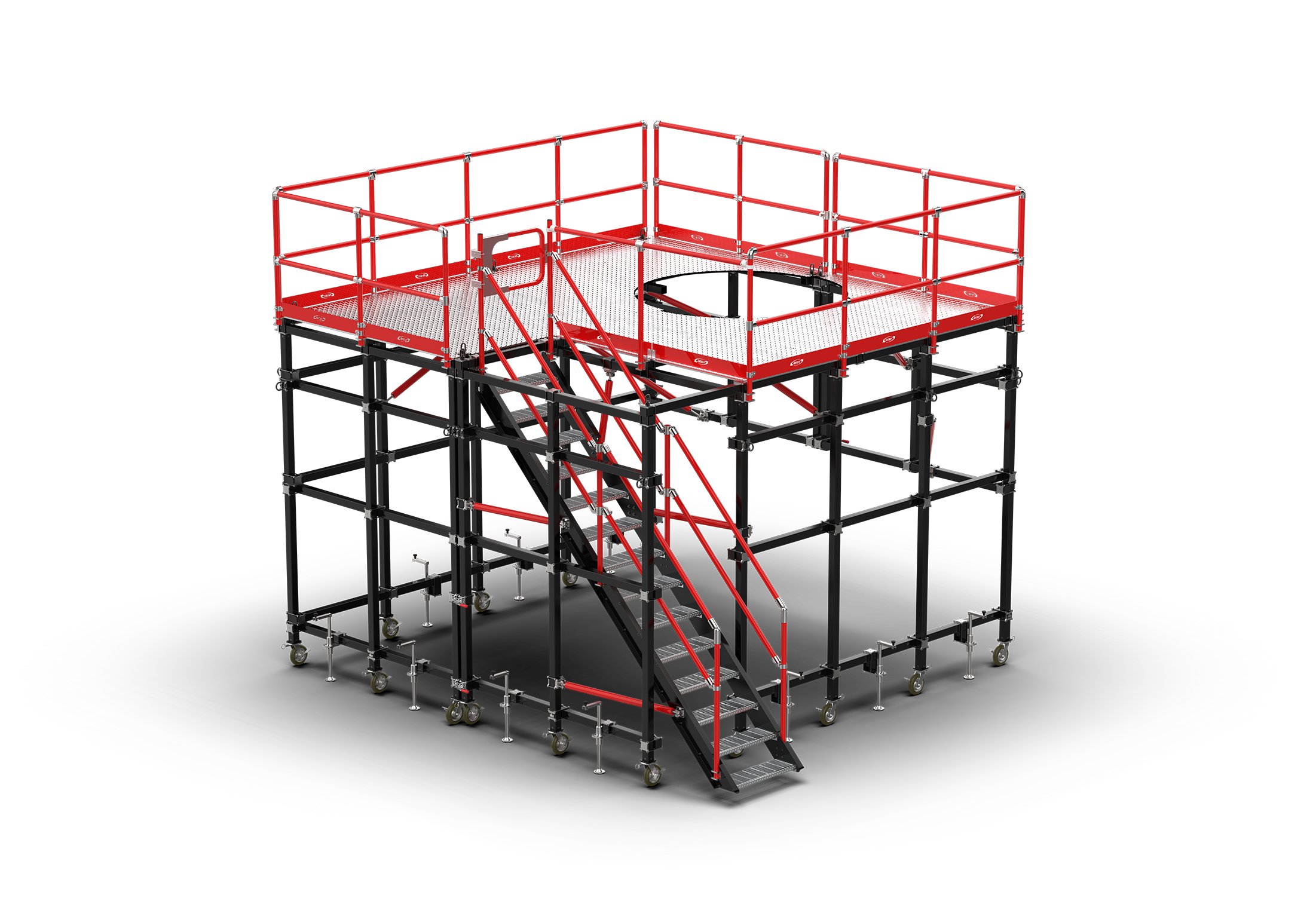
Complex Work Platform
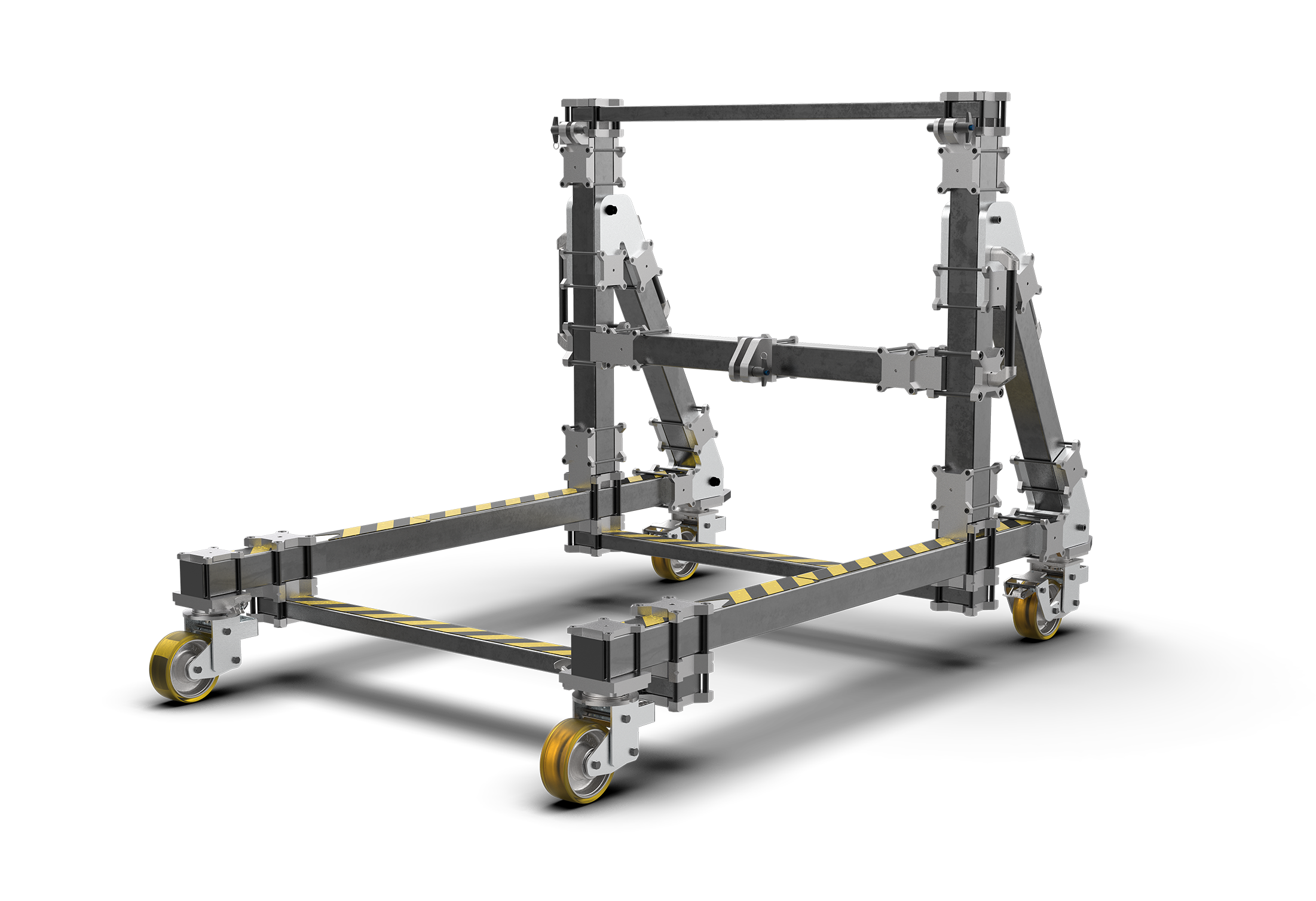
GSE Engine Cart
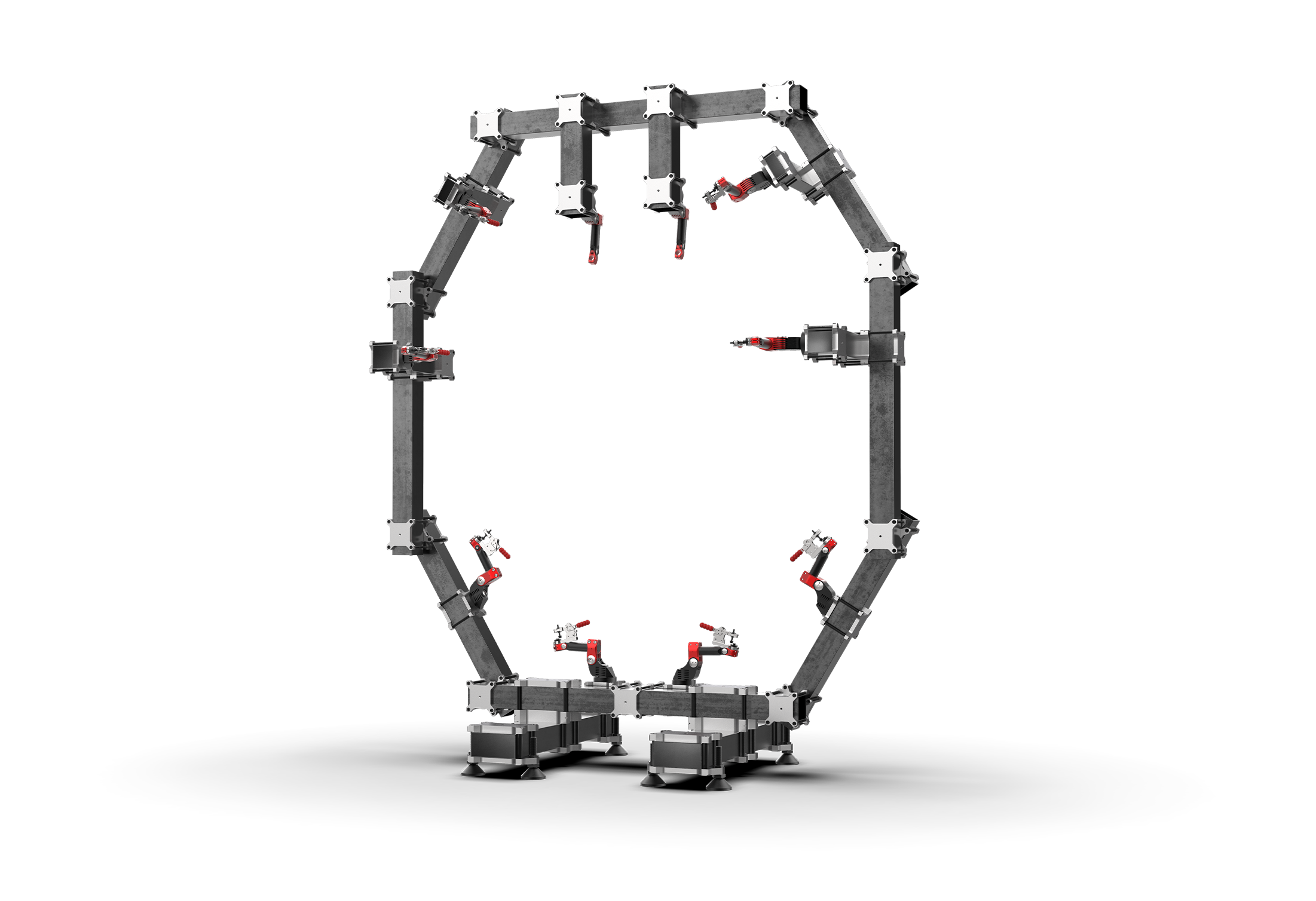
Hexagon Assembly Jig
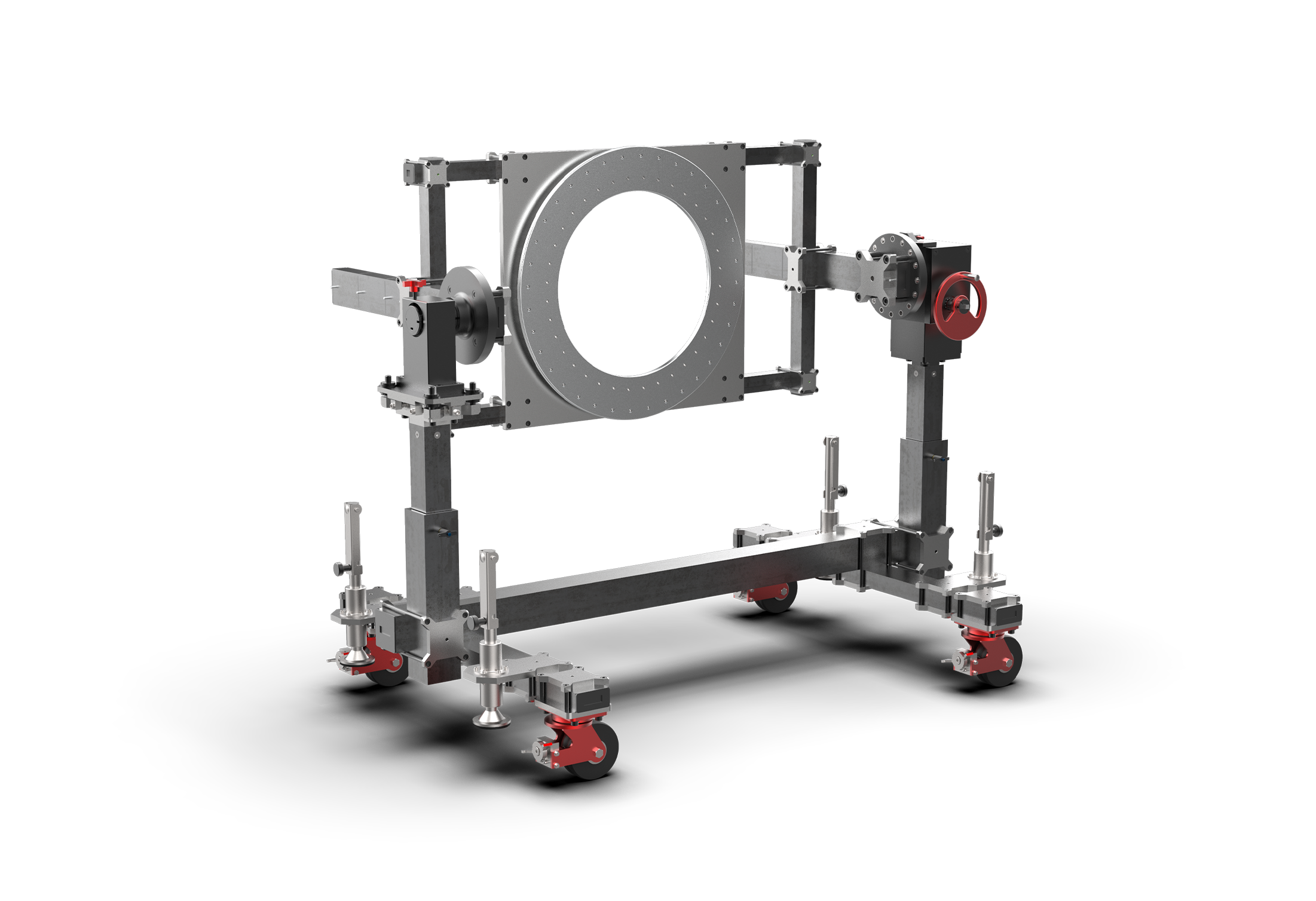
Rotational Ergo Tool
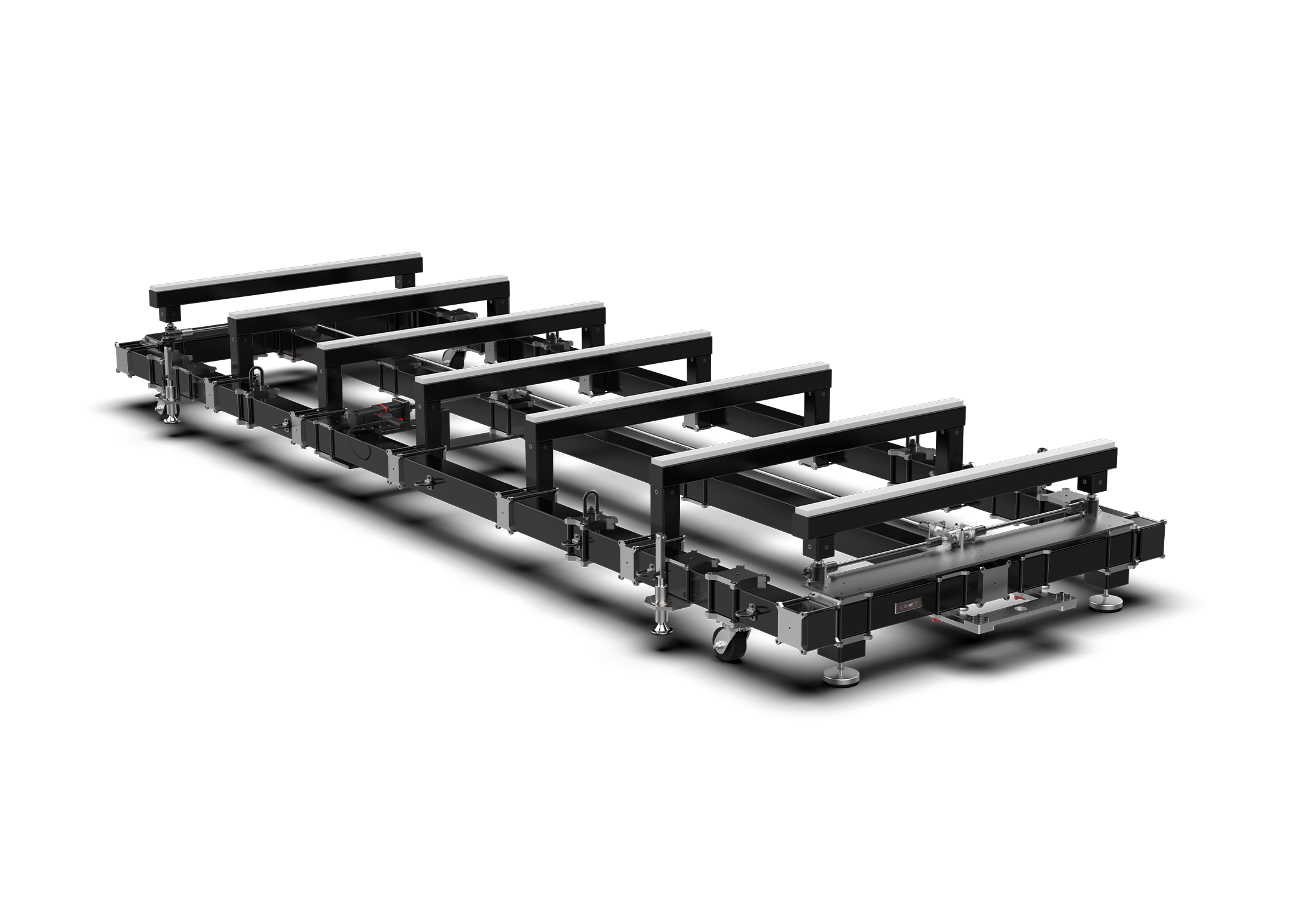
Complex Mechanical Assembly Cart
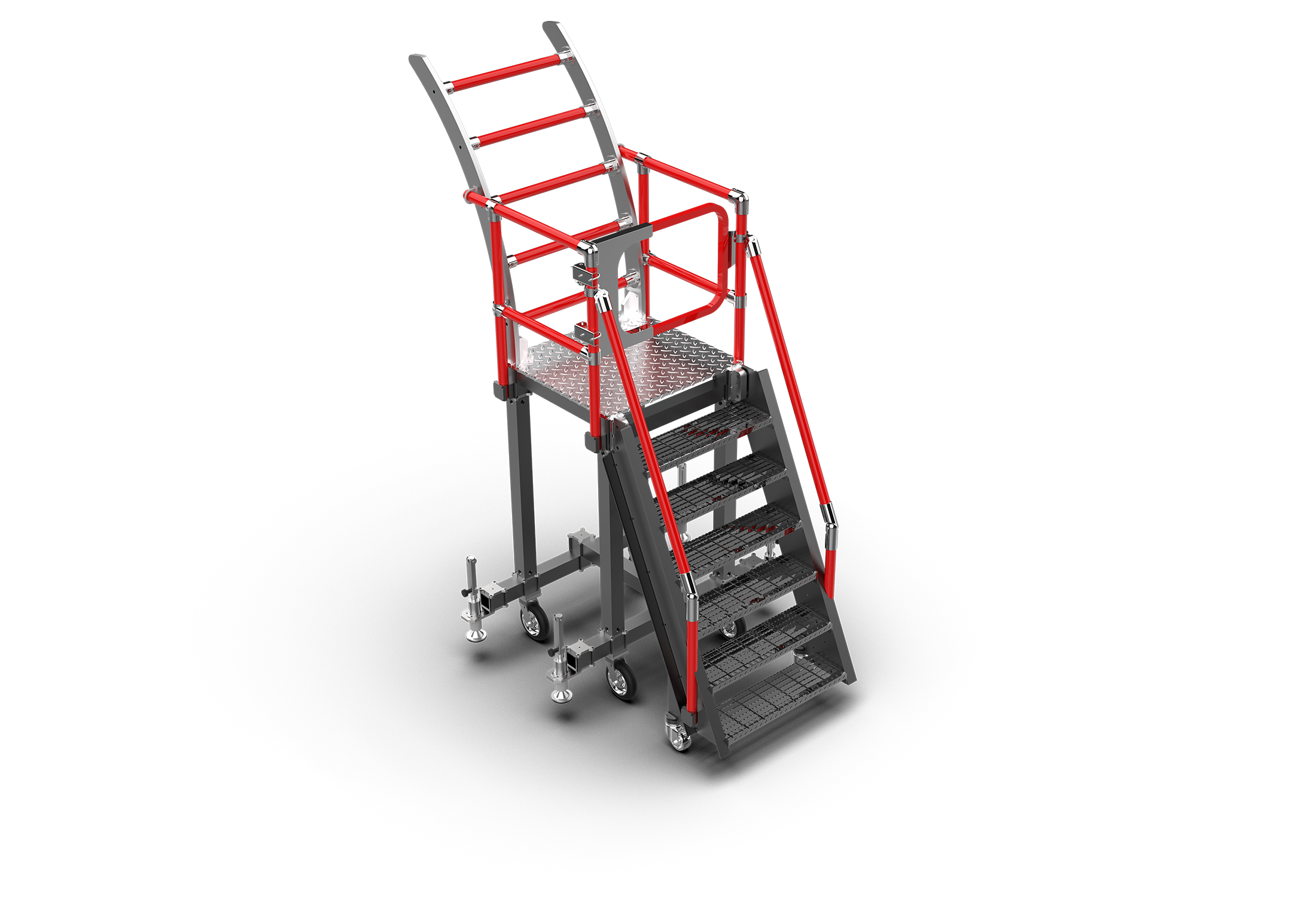
Work Access Ladder
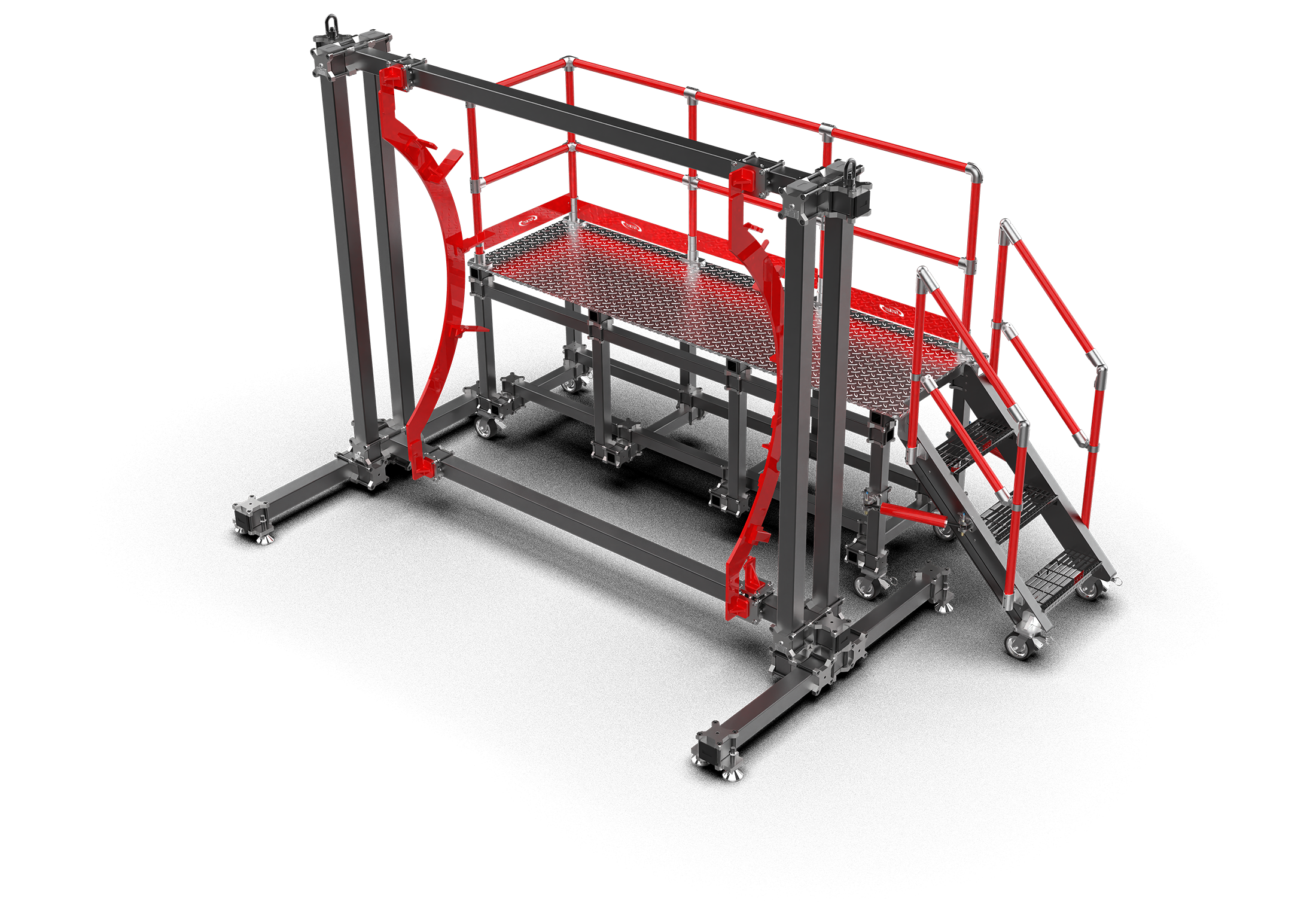
Holding Fixture
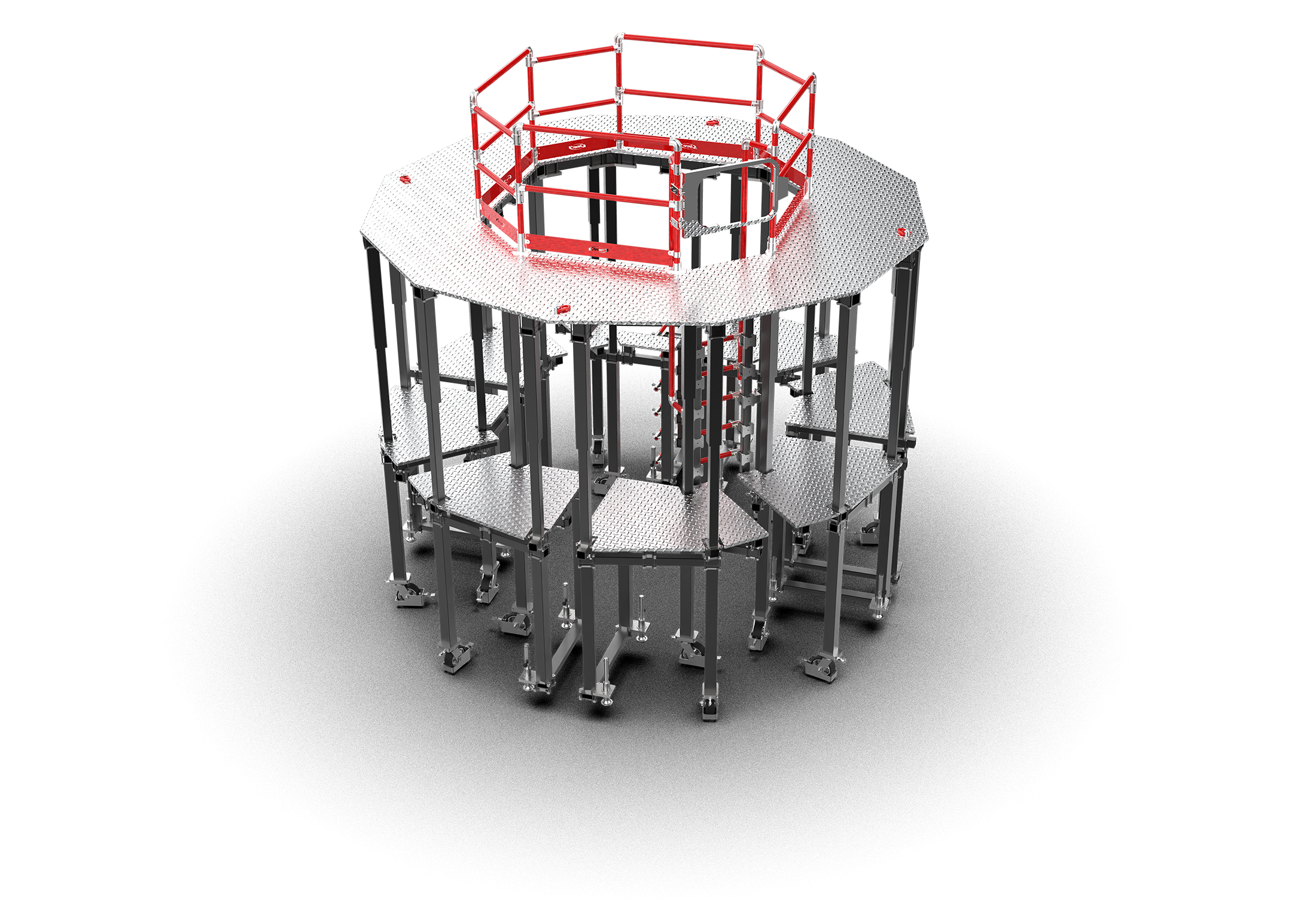
Large Rocket Workstand
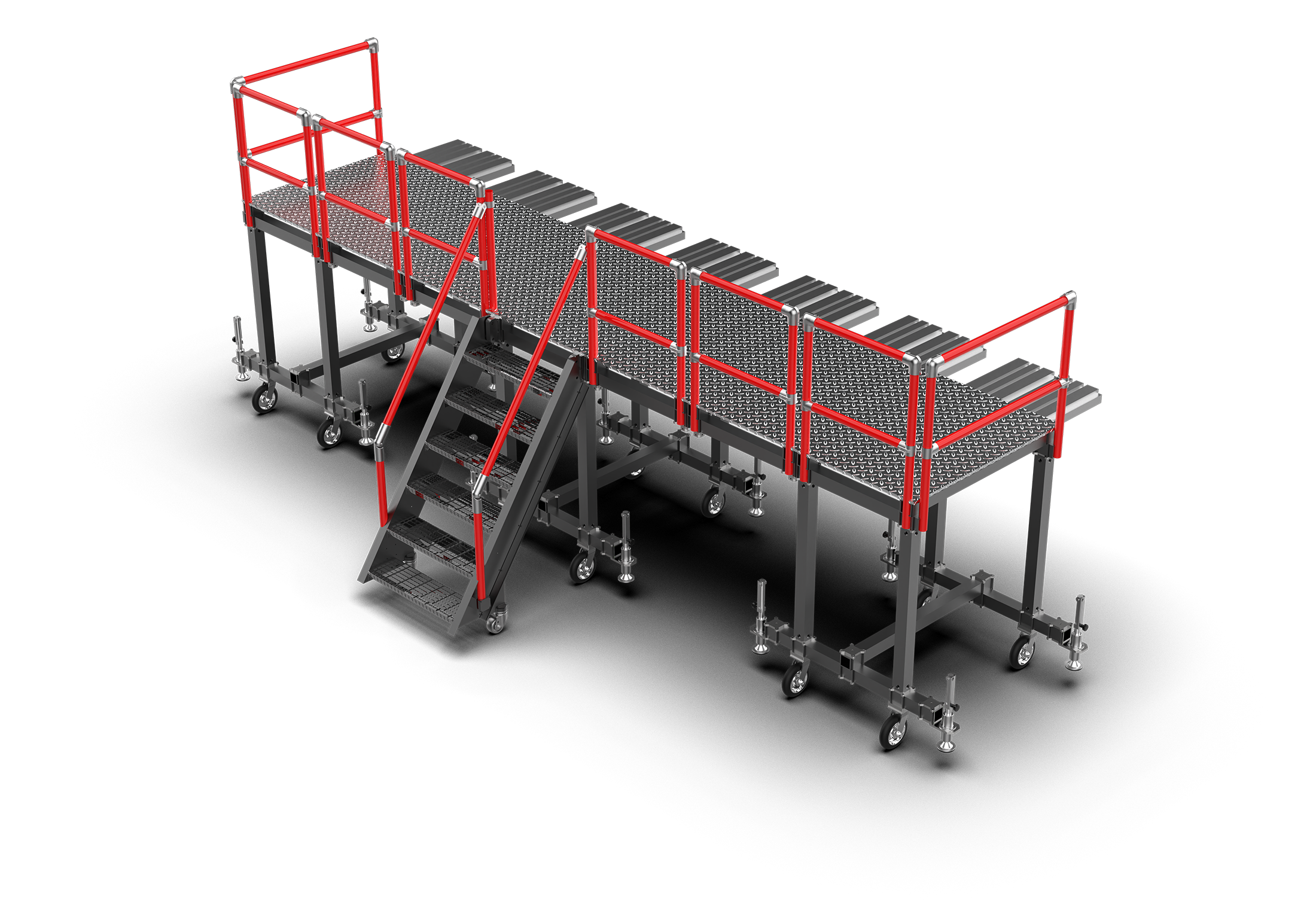
Retractable Workstand
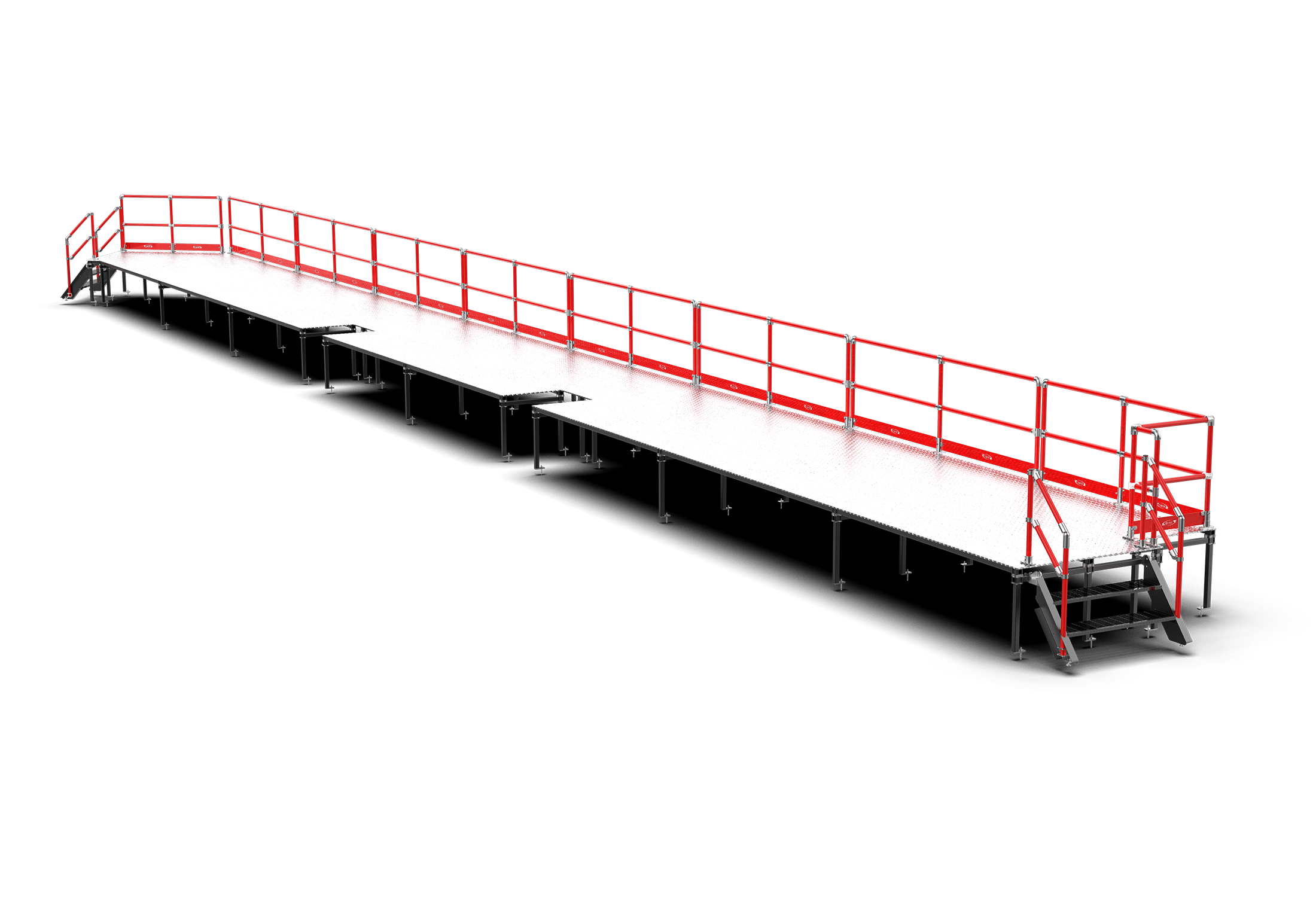
Long Work Platform
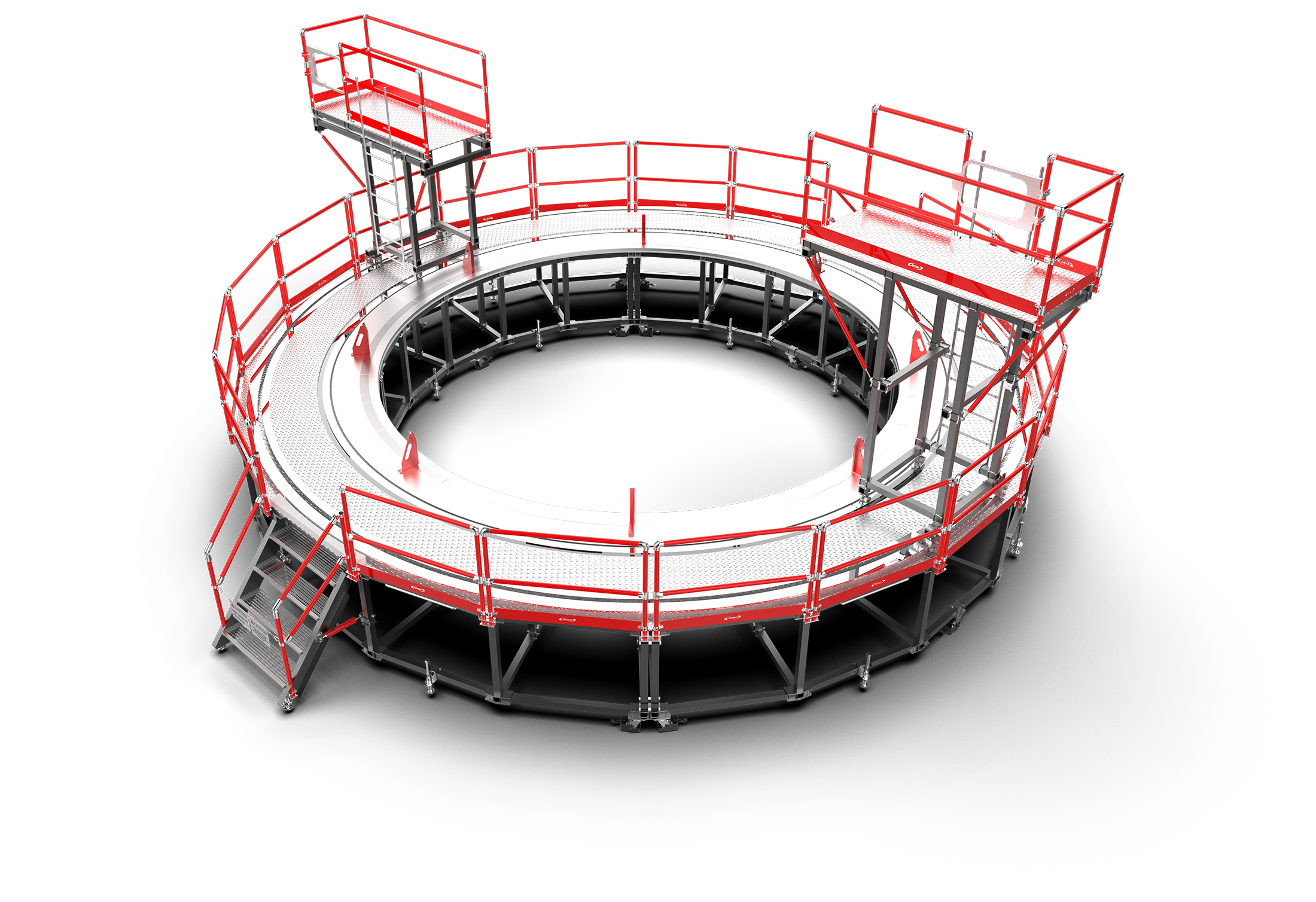
Circular Rotating Platform
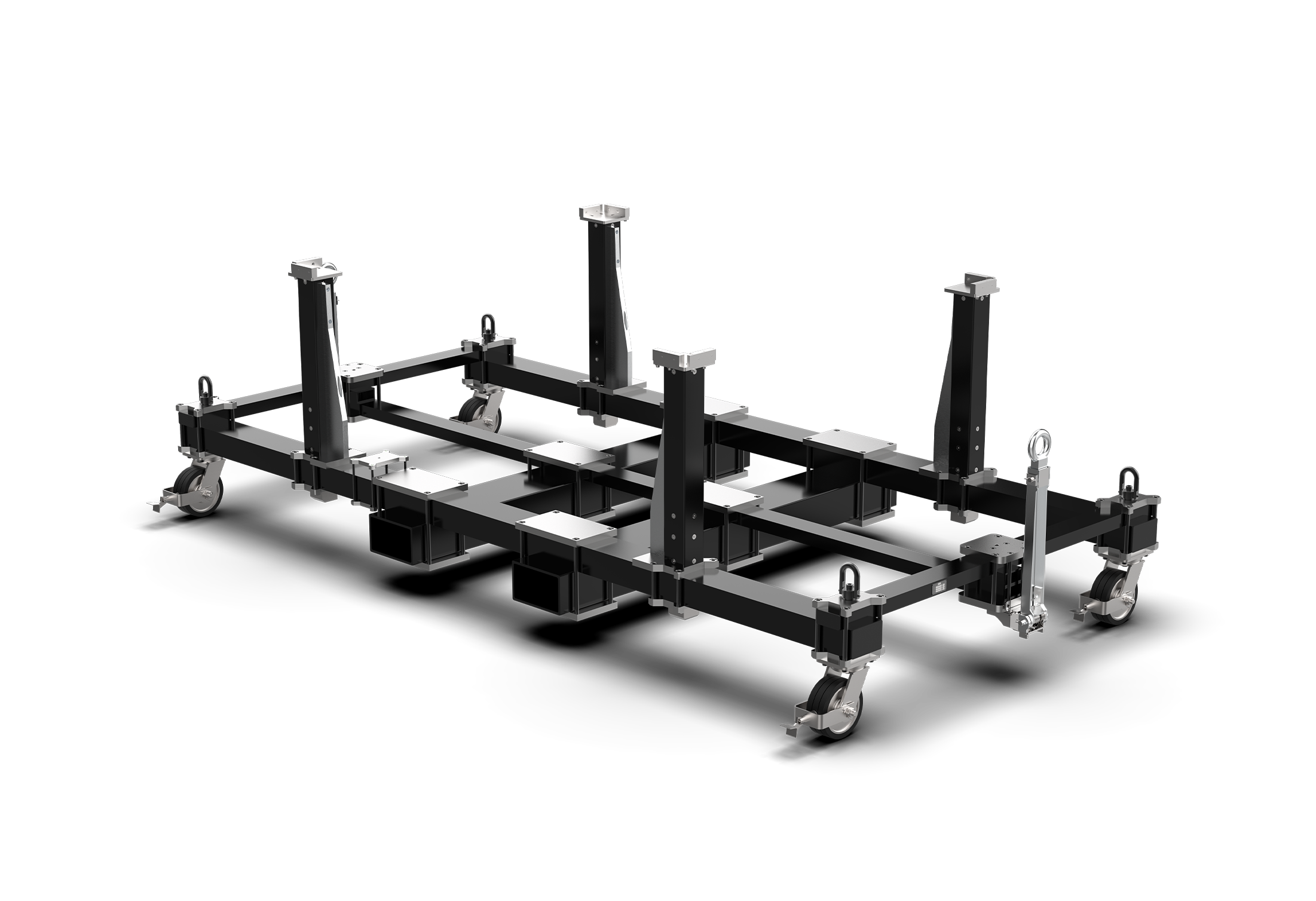
Stackable Tooling Cart
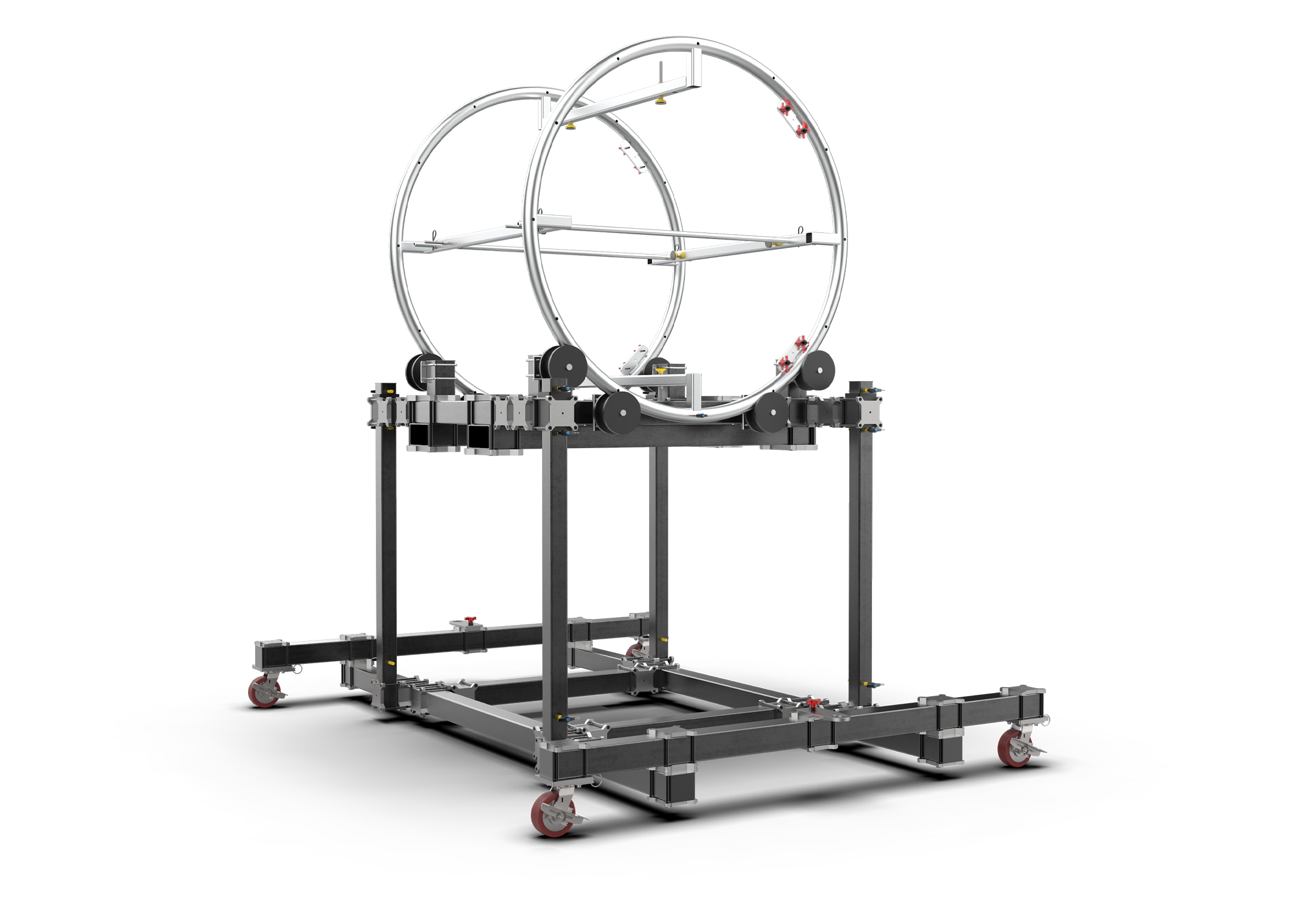
Rotating Wing Holding Fixture

Ergonomic Work Platform
Want to Learn More?
To request the Harcourt® Technical Data Sheet with more information on HBOX™, enter your information below and our team will be in touch with you shortly! Don’t forget to check your spam folder.
"*" indicates required fields
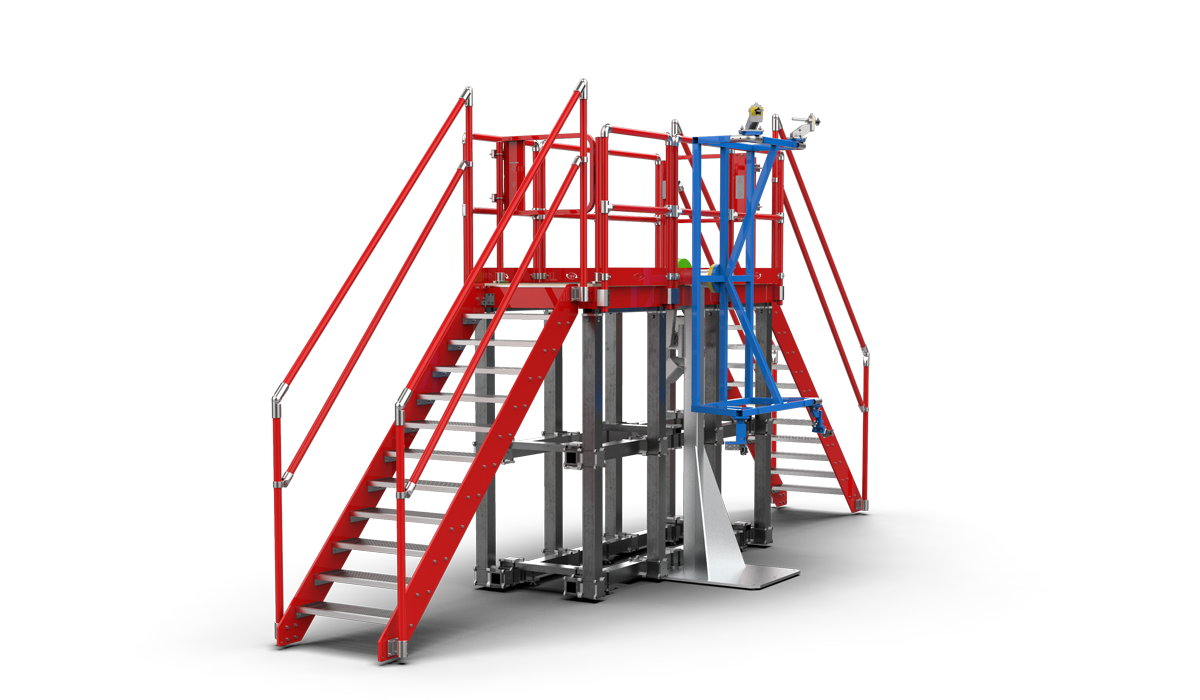